Safety Culture
Keeping Our People Safe
There are multiple hazards associated with our industry – from 1200 tonne compression moulding tools, to operating heavy machinery and moving vehicles to cutting, folding and welding steel. Because of this, we integrate safety into everything we do.
At Cubis Systems, every employee has the right to work in a safe environment and the right to refuse to carry out an unsafe act. The development of a strong safety culture is driven by management and employees at every level. Together, we work towards a common goal – to create a safe working environment where nobody gets injured. Achieving this goal is the number one priority for our business.
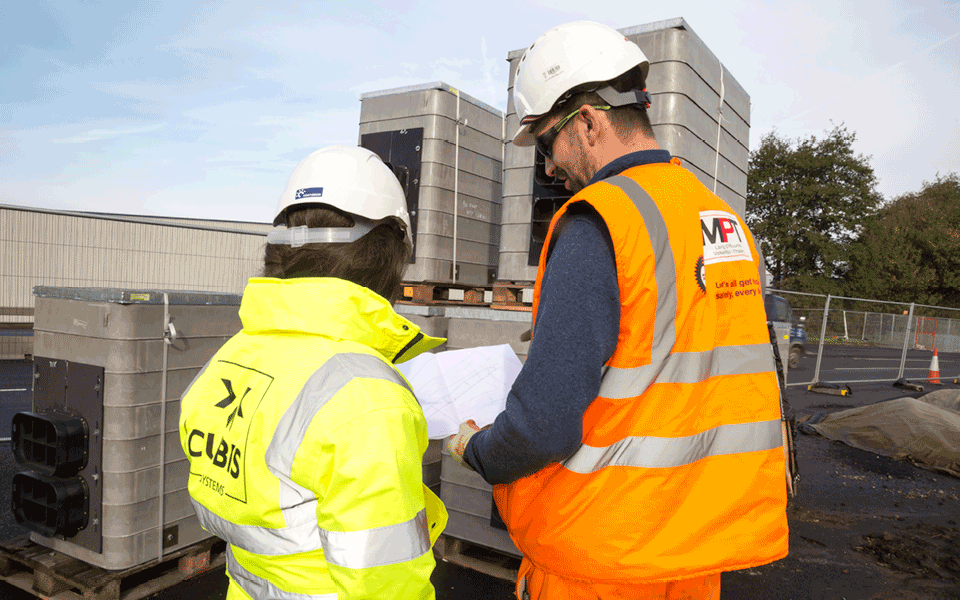
Managing Safety
At Cubis Systems we have a strong safety management structure. Our manufacturing sites have a responsible Safety Officer coordinating and facilitating company health and safety programmes and processes.
The Safety Officer assists operational managers in working to achieve a culture of safety and excellence at every location. This is achieved through the implementation of various safety procedures and programmes, such as regular internal audits carried out by Safety Officers, internal and external transport safety checks and the application of the CRH Fatality Elimination Plan and the ’16 Life Saving Rules’. All employees undergo health and safety induction training, job specific training depending on the role and ongoing refresher training. Good safety practices and safety observations are circulated throughout our company locations as a means of sharing product, material or process best practice or identifying issues which need to be addressed.
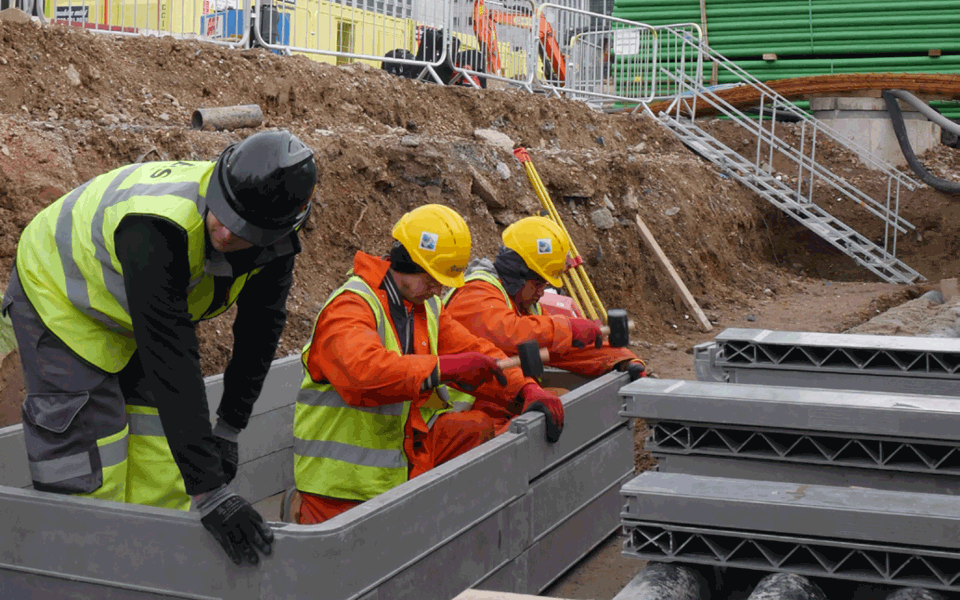
Creating a Safer Industry
All our products are created with the installer and end user in mind.
- Simple, optimised assembly methods require no specialised training and minimal tooling.
- Accessories such as cover lifting keys, chamber access steps and cable management systems ensure safe and convenient access for the end user.
- Lightweight product parts allow for safer manual handling and removes the need for heavy lifting machinery when assembled on site.
In order to ensure best practice during installations our technical team is on-hand to offer site specific installation evaluations and recommendations. Detailed installation instructions are provided with the highest level of health and safety in mind.
Educating and Empowering Employees
At Cubis Systems we recognise the importance of individual behaviours and we empower each employee to be responsible for their own safety and the safety of others. All new employees receive an extensive health and safety induction including an in-depth review of the 16 Life Saving rules, manual handling, safety observations and near miss reporting. Employees receive further training in their specific job roles including equipment usage and safety considerations. We recognise superior safety achievements, rewarding employees for acting safely while also encouraging them to identify and report any safety observations they note. Regular safety meetings with employees take place at all our locations with 97% of employees involved in formal safety climate surveying.
Safety Climate Survey Results
The safety climate survey is a tool used internally in Cubis to gauge the safety culture of our company. Every individual, in every department across each operational site is confidentially asked about their perception of safety practices across the company. Results are reviewed and used to improve our commitment to safety and ensure continuous organisational learning.
The following results indicate employee opinion of safety in the Cubis Systems workplace:
Results |
|
There were adjustments made in the workplace after near misses | 100% |
Health and safety procedures reflect how the job is actually done | 95% |
Identified hazards are acted upon | 99% |
Near misses and potentially dangerous situations are reported | 97% |
Free to bring up safety concerns | 97% |